What Is an Impact Crusher and What Can It Do for You?
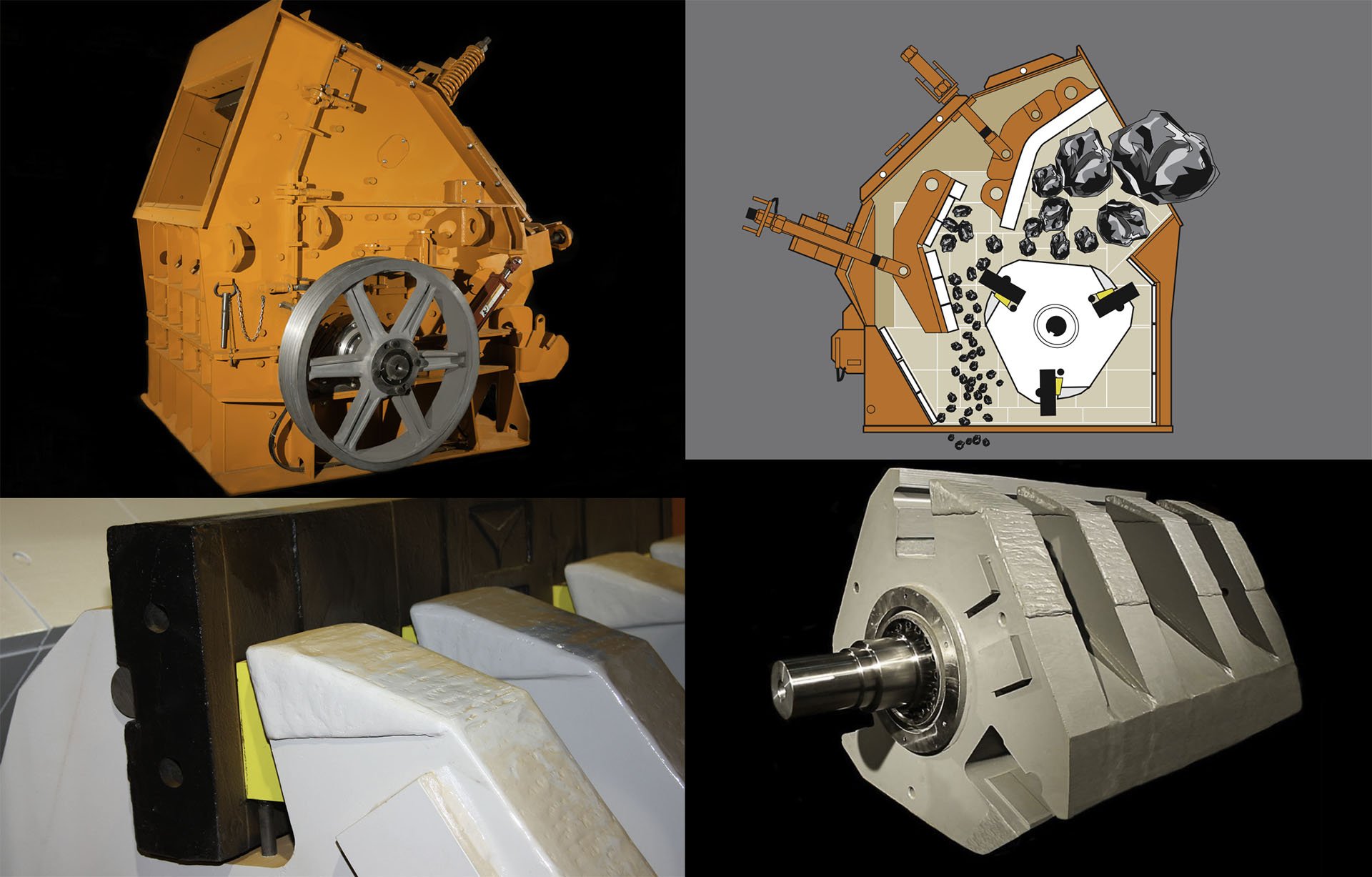
An impact crusher, or impactor, is one of several types of crushing machines, including jaw crushers, hammermills, and cone crushers, that is manufactured for the purpose of processing raw materials, like concrete or asphalt, among many others, to reduce them in size.
Used in a wide variety of applications, including aggregate crushing, asphalt crushing, and concrete crushing, etc., an impactor is unique to its crusher counterparts in that it breaks apart rocks and stones by rapidly striking the material as opposed to utilizing a pressure force.
The mechanical structure of an impact crusher is defined by its rotor, the primary instrument for breaking apart material. The rotor is set among mounted plates, anvils, or aprons, inside a heavy housing; these aprons or anvils serve to bear the impact of the materials being processed and further break them apart.
There are two styles of impact crushers: horizontal shaft impactors (HSI) and vertical shaft impactors (VSI). The distinguishing feature between these two styles is the physical orientation of the rotor within the impactor.
The rotor of a horizontal shaft impactor is oriented horizontally and utilizes blow bars or hammers to strike flowing material with great force in order to break it. Horizontal shaft impactors are useful as both primary or secondary crushers and are able to crush a wide range of materials, from soft rock to much harder materials.
When a horizontal shaft impactor operates, the rotor spins around its shaft at a high velocity. As material flows into the chamber, the rotor’s blow bars repeatedly strike the materials, breaking them apart and sending them into the hanging aprons, resulting in additional reduction.
A vertical shaft impactor’s rotor is oriented vertically, and instead of relying on striking material with great force, it relies on launching material at high speeds to be impacted upon anvils or even other rocks configured around the perimeter of the rotor. Vertical shaft impactors are limited in the feed size they can process and are used as secondary or tertiary crushers only.
When a vertical shaft impactor operates, material is fed into the chamber from above the spinning rotor. The material enters the rotors rapidly moving wings and is hurled outward to be broken upon the peripheral anvils or rocks.
The final size of material being processed by an impact crusher is partially determined by the rotational speed of its rotor. As the rotor operates at higher velocities, material is reduced to a finer and finer specification. Additionally, how closely the aprons are in relation to the rotor can further determine material size; the closer the aprons, the finer the output.
The impact crusher is popular because it can be used for a variety of material processing applications in a variety of configurations, making it a versatile crusher to own. From soft rock to hard rock—as a primary crusher or secondary crusher—the impact crusher can be custom calibrated to ensure your success.
Eagle Crusher UltraMax® Impactors are the most durable and reliable horizontal shaft impactors on the market today. Originally designed to process the toughest high-volume steel rebar with ease, UltraMax® Impactors outperform the competition across multiple applications—aggregate, asphalt, concrete recycling, and more.
Performing the job of a primary and secondary crusher in one unit, UltraMax® Impactors are built for high volume production and ultra-high reduction rations to produce high quality cubical product with minimal fines.
For complete UltraMax® Impactor product specifications, please visit its product page.
Serious Projects Demand Eagle Crusher.
Eagle Crusher consistently leads the industry in new product innovations. We stand by our products with unsurpassed service and support to make your job easier.
Get serious. Get Eagle Crusher.
• Durability and longevity
• 24-hour parts and service
• American made
• Highest productivity and profits
• High resale value
• Celebrating 100+ years of service