Service Questions: Looking Back at over 35 Years of Eagle Service
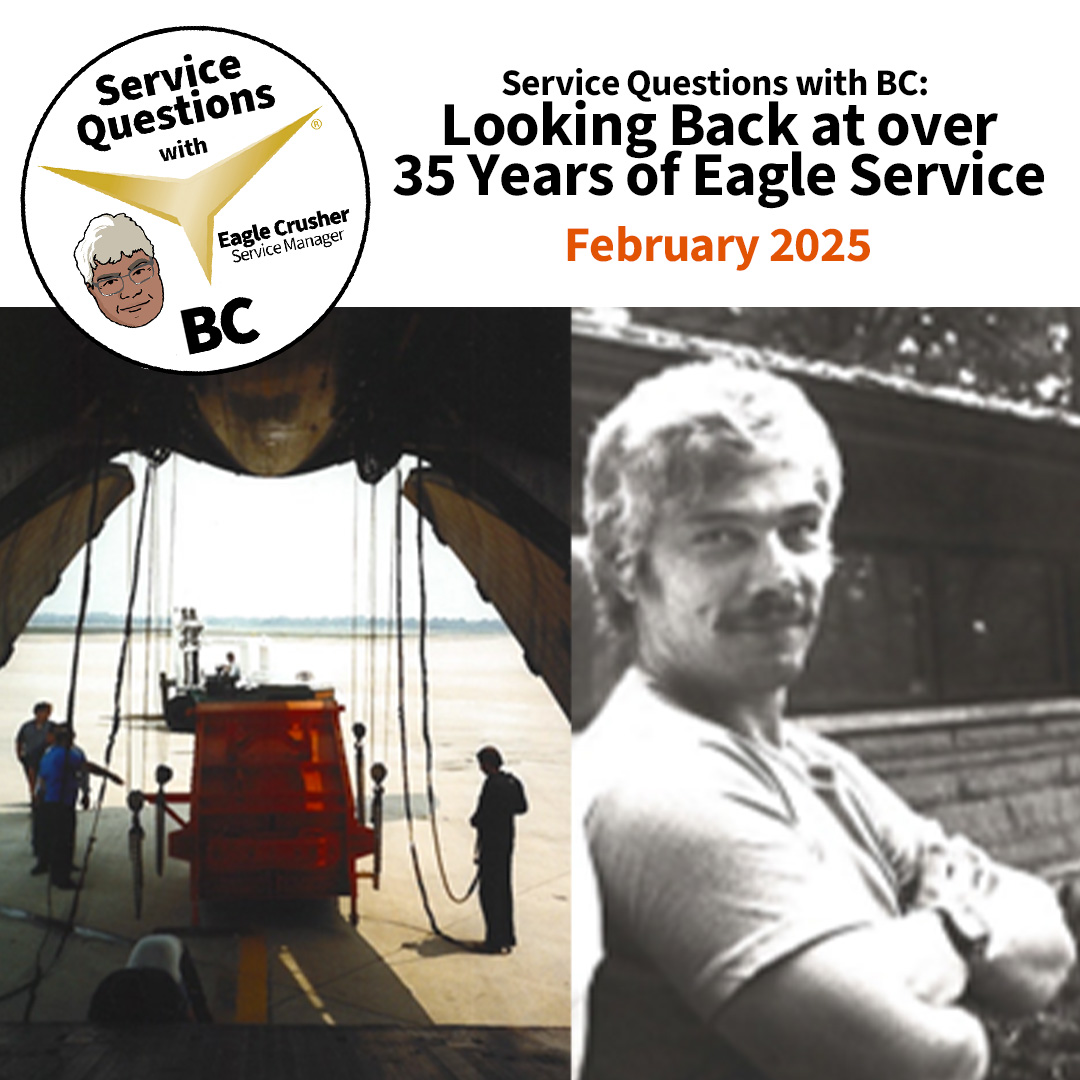
Service Questions with BC: Looking Back at over 35 Years of Eagle Service
For over 35 years, Bill Compton (BC) has been the backbone of Eagle Crusher, setting the standard for exceptional service, leadership, and innovation. As we celebrate his retirement, we reflect on his unwavering dedication, the countless challenges he has turned into opportunities, and the lasting impact he has had on our team and customers alike. BC’s passion and commitment have not only shaped our company’s success but has inspired us all to aim higher every day. BC worked at Eagle Crusher for a total of 42 years, serving as Group Leader over the Jaw Crusher assembly, Cobey composter assembly, and small crushing plant assembly at the previous Galion facility in 1986; temporary Plant Manager at the new, and current, Bucyrus location from 1994 to mid-1995; Service Technician starting in 1991; and finally awarded the title of Service Manager in 2010. Join us in honoring BC’s 15 years of being Eagle Crusher’s Service Manager with 15 facts, stories, and challenges he faced over the years.
Facts from BC’s Service
1) I have had the pleasure of setting up and working the booth for 12 shows. The first was in 1981 and was held at the Astro Dome in Houston, TX; and my last was the ConExpo of 2017 in Las Vegas.
Spectators enjoying the inner workings of Eagle Crusher’s UltraMax Impactor at ConExpo / ConAgg in 1994
2) I installed and serviced the first Eagle 1200 with the newly designed and built Ultramax UM-25 impactor down in Orlando, Florida in 1993.
3) I have worked multiple times with and trained troops from the US Navy Seabees in Mississippi and California on their fleet of 1200-25 CC plants.
Former Eagle Crusher salesperson, Don Bayer on the left and BC on the right in 1992.
Stories from BC’s Service
Throughout his time at Eagle Crusher, BC has set up and/or serviced machines in 34 of the continental 48 states and Hawaii and eleven different countries. The following stories are from those various trips.
4) My first trip out of the US was 20 days in Honduras, in an Army base camp. We set up an Eagle Jumbo 1000 closed circuit plant at a remote quarry in the jungle of Honduras.
BC in blue surrounded by troops of the 13th Corp of Engineers during their New Years Eve celebration.
We stayed in an army tent, slept on a cot and lived with the troops we were training, the 13th Corp of Engineers from Fort Knox. We left on December 26 and spent New Years with the troops in Honduras. Not only did we get to live in the tent with several other troops, but we also got to stomp through the ankle-deep mud each evening to go to the community shower tent. My coworker was leaving the tent one morning to go down to the community latrine area, and as he stepped out of the tent onto the wet muddy steps, he fell. This resulted in a broken wrist, and he spent the next several remaining days of the trip in a cast while out in the jungle.
Eagle Crusher’s Jumbo 1000 Closed Circuit making its way on the dirt road in Honduras.
5) I set up a 1400 Closed Circuit plant in the San Francisco Bay area. They were processing debris from the 1989 Loma Prieta earthquake that hit the Bay area and Oakland, California really bad.
6) I installed several 1400 series plants I went to Taipei, Tiawan and set up a Jumbo 1400 closed circuit plant that included a portable wet screen, screening plant and 2 coarse material screw washers. I went to Kobe, Japan in 1995 and set up a 1400 closed circuit. This machine was part of a large conglomeration of machinery that was cleaning up and processing debris from the Great Hanshin Earthquake that occurred on January 17, 1995. I went to the Greek island of Cyprus and installed a Jumbo 1400 Open Circuit plant.
BC standing in front of the panel for Eagle Crusher’s Jumbo 1400 closed circuit in Taiwan.
7) I was involved in the loading of six (6) Russian Ilyushin, IL-76 freight airplanes at Rickenbacker AFB, Columbus, Ohio.
News article from the local Galion Inquirer on July 21st, 1992.
This made the local news as this was the first time that Russian aircraft had ever landed in the United States. Then I and one of Eagle Crushers salesmen, Don Bayer, had the pleasure (if you want to call it that) of riding for 20 plus hours in the cargo hold of the sixth plane full of equipment to Russia.
The hood of the Eagle Crusher’s impactor being loaded onto one of the freight airplanes.
Our accommodations for this flight were a couple of pillows and blankets and a sheet of plywood we scavenged from a plywood shipping crate we dismantled and laid on top of a group of 5-gallon buckets of highway striping paint. This little trip took us from Rickenbacker AFB in Columbus (this is now a commercial airport) to our first stop for fuel in Gander, New Finland. After re-fueling we then proceeded to Shannon, Ireland and made a second fuel stop. It was then on to the next fuel stop, this time at Moscow, Russia. After re-fueling here, it was one more several hour flight North to our destination in Raduzhny, Siberia. Once we landed and the equipment was all unloaded, the airport was shut down as the purpose of the job was to pave the runways of this airport.
The Eagle Crusher system setup in Siberia.
8) I installed and serviced a 1400 closed circuit plant at a commissioned Uranium processing facility, Fernald site, near Cincinnati, Ohio. This was a total white suit, double layer glove, boot covers, and respirator required job. We all also had to wear a radiation monitor all day and have it read every day before we could exit the site. I Installed and trained people on a 1000-15 CV plant at the Paducah Gaseous Diffusion Plant in Paducah, KY. This was also a Uranium enrichment facility, so again radiation was a concern. It was originally determined by the contractors that this job was going to require all personnel to wear a full-faced respirator but by the time the startup actually got scheduled they had relaxed the requirements, and we only had to wear a N-95 mask.
Eagle Crusher screen in Cincinnati, OH.
9) I traveled to an extremely small and remote town in Panama to assist a group of Canadian contractors with the installation of a Jumbo 1200.
The Eagle Crusher Jumbo 1200 setup in Panama.
I got the shock of my life one day as we were digging through one of their spare parts boxes for something and I moved a box only for a scorpion to run across my hand. I was done at that point!
10) I had the experience of going to Sudbury, Canada to a huge gold mine in the dead of winter to work on an Eagle Low Profile underground jaw crusher. The crusher was underground at about 3800 feet. It was minus 35 degrees on the surface that morning and so cold that my car wouldn’t start when I needed to leave the motel so I had to call for a cab to take me to the mine. Once there, they took me down to the crusher via an elevator and once at the crusher it was 70 degrees underground. Quite an experience that I don’t care to do again.
11) I traveled to Honolulu, Hawaii in the early 1990’s to install a Jumbo 1400 closed circuit unit. Then, I returned in 2019 to install a new screening plant for this same customer that was now replacing their worn out 1990’s screen plant.
The Eagle Crusher Jumbo 1400 Closed Circuit setup in Hawaii.
Challenges from BC’s Service
Anyone who’s worked in the service industry knows that things rarely go exactly as planned. From unexpected hurdles to last-minute changes, the fast-paced nature of service demands adaptability and resilience. Yet, it’s in these moments of challenge that true growth happens. Every obstacle presents an opportunity to learn, innovate, and refine how we serve our customers.
12) Several years ago, we had a long-standing repeat customer out in New England that bought a new 1000-15 CV. He kept having issues with his diesel engine and about every 1500 to 2000 hours the engine would start smoking and burning a lot of oil and the piston rings would be worn out.
Image of oil pooling under the engine.
We and/or the engine manufacturer would step up and rebuild or replace his engine and a few months later the same thing would happen. After about 3 engines had failed it was finally discovered that the air intake piping between the engine air filter body and the intake of the engine was a steel pipe. This pipe was rusting inside. The rust scale would then flake off and since this was between the filter and the engine itself, those rust particles got ingested by the engine, thus destroying the piston rings and cylinder walls. The engine’s manufacturing team converted to an Aluminum pipe so it couldn’t rust.
13) Back around 1999 to 2000, we started incorporating the feature to shut the diesel engine down with the emergency stop buttons on our control panels. However, one of, if not the first, units that shipped to our new England dealer was equipped with this feature and caused havoc at start up. The 1200 CC was shipped to an island via a barge so access for the dealer was via a ferry.
An example of the panel layout in the early 2000s.
They attempted a startup but could not get the diesel engine to start. Since this feature was new to everyone, no one thought of having them check the emergency stop buttons for one being activated. Our dealer called in an engine manufacturer technician to assist and involved a second service vehicle having to take the ferry to the island. The engine tech traced the no start issue to the tripped E-stop button and upon resetting the button the plant started up as it should. This then drove us to incorporate an alarm that would sound if the diesel engine attempted to be started while one of the e-stop buttons was pushed in and activated.
14) In the early years of offering a variable frequency drive (VFD) on our machines to control feeder speed, we routed the shielded speed potentiometer cable along with other power cables along the chassis. To save wire clamps, weld studs and creates a compact wire run; we mounted the shielded cable in the same wire clamps that was securing 480-volt motor power cables.
An Eagle Crusher panel from 2003.
After delivery of the machines and putting them into service, we were being bombarded with phone calls about VFD’s not working. We initially assumed that we had received faulty VFD units and so we sent replacements. When the replacement VFD’s didn’t resolve the issues, someone in the field decided to try rerouting the VFD shielded cables. Just relocating this shielded cable 4 to 6 inches away from the 480-volt power cable was the solution to eliminating the electrical interference that was causing the VFD’s to fault out and shut themselves down. This then was incorporated as standard installation practice here for several years.
15) Many years ago, we used fuses in our electric panels as the protection for the circuit wiring and as short circuit protection. We had a couple of catastrophic panel failures due to arc flash. I determined that the end users were just allowing their spare fuses to sit in the bottom of the electric panels until they decided they needed to use them.
An image of the state the client left their panel.
It was determined by a third-party investigator that these fuses sat in water and the water got inside the fuse barrel. Once they installed a fuse that had water intrusion in it, the fuse got hot from normal circumstances and that water turned into steam creating a small bomb out of the fuse. When the fuse finally exploded from the steam build up, it fractured and damaged the fuse block it was inserted in and allowed a short circuit either between power phases or power to interior panel ground.
Honoring Legacy
As we look back on 42 remarkable years with BC, we are reminded of the countless ways he has shaped our journey. From leading by example to navigating challenges with unwavering grace, his contributions have left an indelible mark on our team, our customers, and our company’s legacy. While it’s impossible to quantify the impact of four decades of dedication, one thing is certain: his leadership has built a foundation of excellence that will continue to inspire us for years to come. Here’s to celebrating the past and embracing the future with the lessons and values BC has instilled in all of us.
Make sure to follow along with more “Service Questions” where Eagle Crusher’s Service Technicians answer some of the frequently asked questions about preventative maintenance and more.