Preparing Aggregate for Crushing
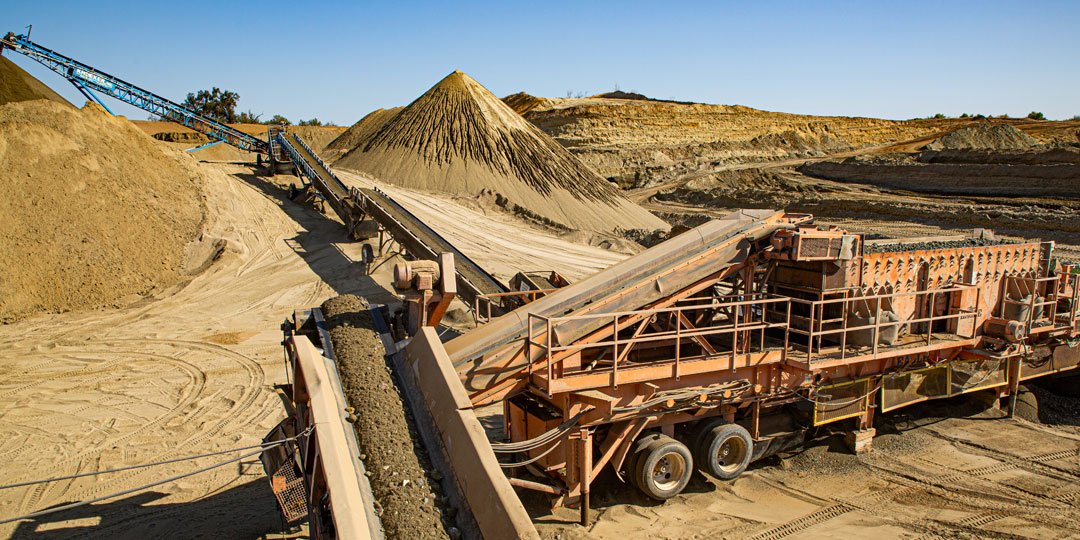
It is often said that a job is always cheaper to do right the first time, and in the world of aggregate production and concrete or asphalt recycling, efficiency is the final word in making a profit.
From quarry to crusher, every moment matters in producing a quality product at the right size in ample amounts, and there are several key decisions a producer must make when it comes to properly preparing aggregate for a crushing job.
As far as getting off on the right foot is concerned, the initial blasting or drilling of rock usually offers the best opportunity for preparing aggregate for crushing. A calculated and adequately executed excavation effort can mean procuring rock that can be fed directly into a crusher hopper without further reduction.
On that subject, it is important to note that the size and capability of excavators and loaders can play a key role in streamlining a crushing operation even further. An excavator or loader with a larger capacity for transporting aggregate can result in less time wasted traveling back and forth.
This is why portable crusher plants are particularly valuable on job sites like a quarry—the closer the actual crushing can be to where the aggregate is blasted or drilled, the less transportation equipment will be needed to move the rock.
It is important to never feed larger rocks into the hopper of a portable crushing plant that could clog or jam the machine. If larger aggregate has been procured that is questionable as to whether or not it can successfully be crushed, it is always best to err on the side of caution and fracture the rock into smaller pieces using auxiliary equipment before feeding it to the crusher.
This situation is where choosing between a loader or an excavator to feed aggregate can be an influential factor in your crushing operation. With a loader, it can be difficult to gauge the size of aggregate in the bucket whereas using an excavator can help control the size of rocks entering the hopper.
One other variable to consider in preparing aggregate for crushing is dust suppression. The blasting, drilling, loading, and feeding can generate a lot of aggregate dust that can introduce unnecessary wear on equipment as well as creating a hazardous work environment. Utilizing dust suppression tools like sprinkler systems can go a long way in controlling damaging variables on the job.
If you are interested in learning more about how you can properly prepare aggregate for your crushing operations, we encourage you to contact our team to speak with an Eagle Crusher representative who can help guide you through these important decisions.
Serious Projects Demand Eagle Crusher.
Eagle Crusher consistently leads the industry in new product innovations. We stand by our products with unsurpassed service and support to make your job easier.
Get serious. Get Eagle Crusher.
• Durability and longevity
• 24-hour parts and service
• American made
• Highest productivity and profits
• High resale value
• Celebrating 100+ years of service