Service Questions: How to Avoid Material Contamination
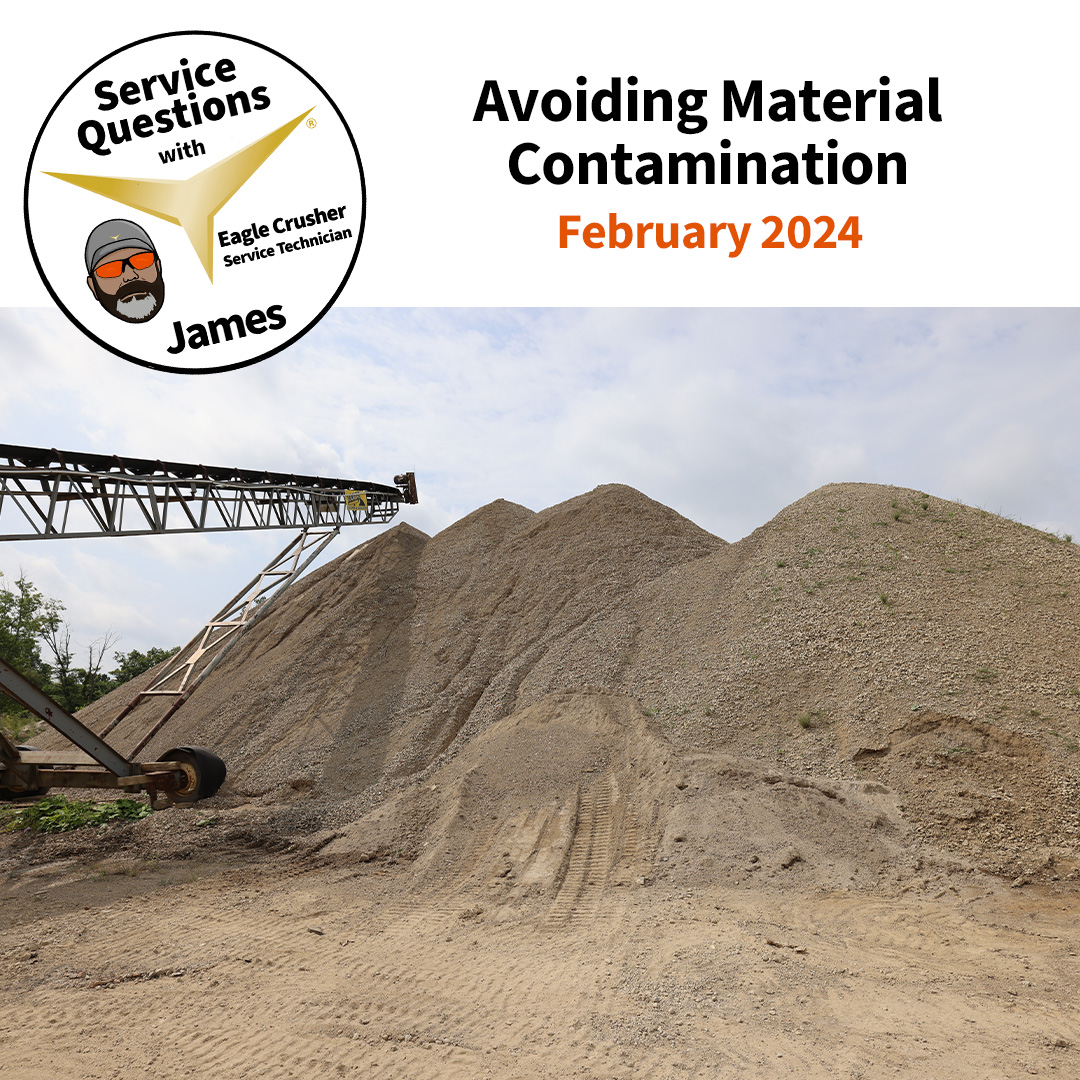
Service Questions with James: How to Avoid Material Contamination
Whether you’re an aggregate producer or involved in concrete and asphalt recycling, the efficiency and longevity of rock crushing equipment plays a pivotal role. However, this crucial machinery can face a silent adversary that can jeopardize the performance of your operation – contamination. The inadvertent mixing of improperly sized products can lead to a cascade of issues, possibly compromising the integrity and functionality of construction materials. This misstep can not only hamper the structural stability of the final product but also poses risks to the machinery, such as rock crushers and concrete mixers, tasked with processing these materials. Avoiding contamination of material sizes requires meticulous attention to detail during the sorting and processing stages, which James will now examine.
Preventing your stockpiles from being contaminated.
Many rock crusher users are producing several products at one time. If the proper components in the screening portion of your crusher are not in place, this could cause your stockpiles to be contaminated with the wrong-sized product. It is also important to match your impactor setting with the screen cloth you have installed on your screening unit. Let’s go over the different ways you can avoid material contamination.
Setting the impactor curtain correctly to achieve the best results.
Most horizontal shaft impactors (HSIs), including Eagle Crusher’s UltraMax® impactors, have a primary and a secondary curtain to properly size material before the screening process. It is important to generally have your curtain set to a 3-1 ratio between the curtain and the edge of the blow bar or hammer, meaning your primary curtain (top curtain) should be set 3 times what you have the secondary curtain (bottom curtain) set at. As an example of the 3-1 ratio, if you are trying to achieve 1 ½ ‘’ minus product you would generally set your secondary apron at 1 ½ ‘’ to 2’’ and your primary apron at 4 ½ ‘’to 6’’. Contact Eagle Crusher’s service team, your local Eagle Crusher dealer, or your owner’s manual for specific measurements.
It is also important to monitor the setting as crushing will wear down blow bars and curtain liners, increasing the gap between the two over time. Eagle Crusher UltraMax® impactors include an inspection door that can be opened after the plant has been brought to a complete stop and locked out and tagged out to ensure the proper settings are maintained.
Using the proper screen cloth sizes for the products you are trying to achieve.
There are so many different sized products you can make with your crusher. Eagle Crusher equipment generates an abundance of different products and to name them all would be short of impossible. It is important to know what size of products you want to achieve and have the correct screen cloths installed properly. This is important so that you can provide the best quality of material to your customers.
Eagle Crusher’s sales and service teams can help you in deciding what screen cloths you need to achieve the highest tonnage and the best results of production and products your crusher can provide.
Preventing dust on your crusher.
Having a large amount of dust while in operation can cause issues not only with the operator’s health and visibility, but also with clogging the air filter on your engine and causing wear to belts and other components.
Make sure you are using the spray bar, typically located on the top side of your impactor. This spray bar is designed to spray water into your impactor to lower the dust levels while crushing.
Keep the rubber skirting on your discharge conveyor firmly up against the discharge belt. This will help keep the dust levels low in the discharge section under your impactor.
Other potential issues
If you find yourself having other issues, Eagle Crusher’s service team is available to help troubleshoot. Additionally, you can send in your questions for an upcoming “Service Questions” or check out the previous “Service Questions”.
Enhancing Operational Efficiency
Concluding our exploration into the world of rock crusher efficiency underscores the significance of mastering techniques to prevent material contamination. With the insights shared in this blog, operators can approach rock crushing operations with newfound confidence to navigate potential challenges. As we chart a course towards continuous improvement, let the lessons here become a cornerstone for success in your crushing endeavors and transform downtime from being a frequent guest to a rare visitor in your industrial landscape. Stay tuned for next month’s feature as Eagle Crusher’s Service Technician, Louis, guides us through the art of preventative maintenance for diesel and electric engines. For any questions, our service team is readily available to address your questions.