Minimize Costly Downtime While Crushing
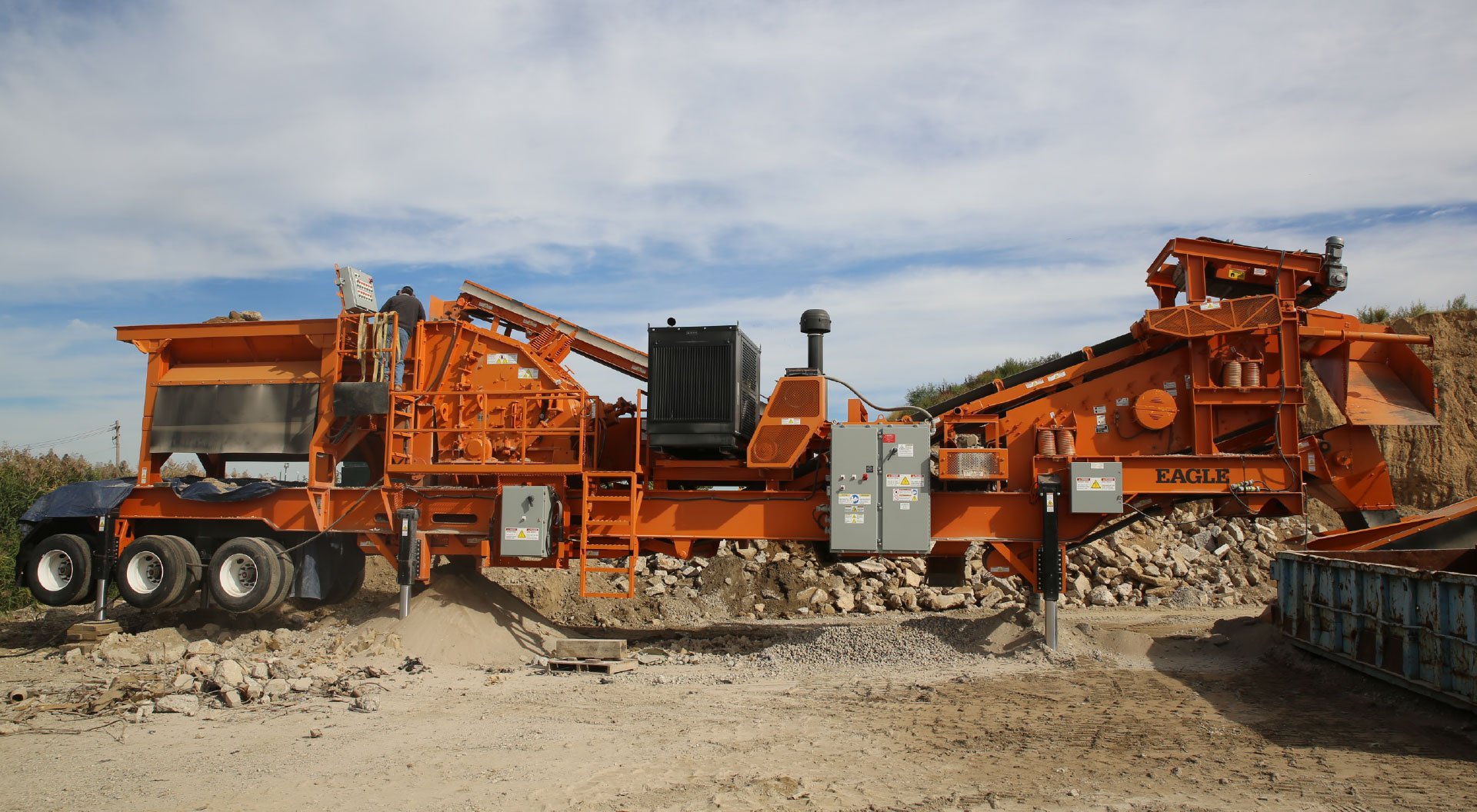
In any crushing operation, your business is doing its best when your crusher plant is running exactly how you want it. However, whether as a result of operator error, cutting corners, or just bad luck, it is inevitable that unexpected downtime will occur, bringing your crushing job to a grinding halt and your profits along with it.
The good news is that there are measures that you can take to minimize these types of incidents from happening, like employing faithful maintenance practices and following proper safety procedures. Investing the time upfront can save you from the heavy expenses associated with needless downtime and will keep your team up and crushing.
As a first step in the defense against downtime, your team should start by exercising preventative activities; these measures can often be perceived as optional but should not be discounted as such. In fact, it may be best to consider preventative habits as the firm foundation from which your downtime minimization efforts are able to thrive.
Examples of preventative routines include simply following proper safety procedures to ensure that team members are able to operate the crusher in good health and to avoid ceasing crushing operations due to an unexpected injury. Just as well, it is crucial to conduct daily inspections of the crusher to ensure the machine itself is in quality working order.
The next step to take in minimizing downtime is employing predictive maintenance; here, teams can use aggregated performance data to track and predict when downtime incidents are mostly likely to occur in order to resolve issues before it becomes too late. If your team is not tracking operational performance, it is recommended that you begin logging this key data.
Knowing how quickly parts and fluids of your crusher plant wear down and how often they need to be replaced can be extremely valuable in the battle against downtime. Additionally, your crusher plant likely operates in unique environmental conditions; tracking its performance against industry averages as you tweak important variables can improve operations.
Unfortunately, practicing preventative and predictive habits can only do so much to mitigate the possibility of downtime. Inevitably, it comes for us all, and it will happen to you. When this moment arrives, your team should be ready to perform reactive maintenance in order to address what could be a costly failure as quickly and effectively as possible.
It is essential to invest in the comprehensive training of your team members. Equipment failure most often rears its head when crushing machines are pushed past their limits. Proper training can combat crushing equipment overload and can also enable team members to adequately address downtime incidents without making the situation any worse.
If you and your crushing team would like to learn more about valuable maintenance habits and best use practices for your crusher, we recommend that you contact our Eagle Crusher service team. Also, because it is important to keep your parts in good condition, we encourage you to contact our parts team to discuss developing an effective replacement schedule.
When all is said and done, one of the best steps you can take to minimize costly downtime at your crushing site is by fostering a diligence among your team. By excelling in preventative, predictive, and reactive maintenance, your team will be well-equipped to face the inevitable—all the while your crusher will be running and preserving your profit.
Serious Projects Demand Eagle Crusher.
Eagle Crusher consistently leads the industry in new product innovations. We stand by our products with unsurpassed service and support to make your job easier.
Get serious. Get Eagle Crusher.
• Durability and longevity
• 24-hour parts and service
• American made
• Highest productivity and profits
• High resale value
• Celebrating 100+ years of service