Minimizing Downtime to Maximize Profits
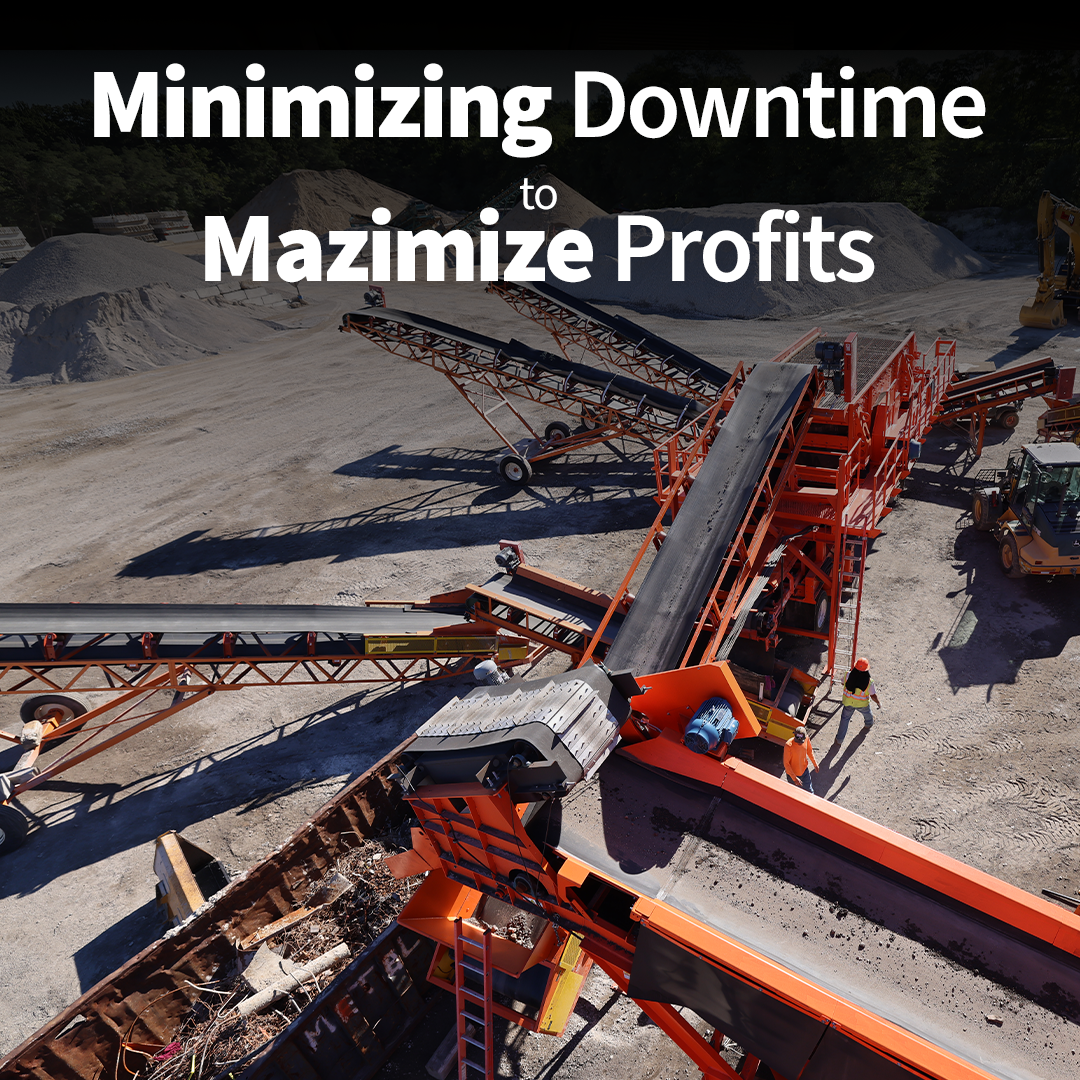
Minimizing Downtime to Maximize Profits
In the world of crushing operations, the height of success is reached when your crusher plant operates seamlessly, aligning with your every expectation. Yet, there remains an inescapable truth: unexpected downtime, born of operator error, shortcuts, or simple bad luck, can swiftly bring your crushing endeavors to a grinding halt, carrying your profits away with it. Do not quarry worry, for there exists a silver lining. By embracing steadfast maintenance protocols and upholding stringent safety measures, you have the power to significantly reduce the occurrence of such disruptions. This initial investment of time and dedication promises to not only shield you from the weighty expenses tied to needless downtime but also to ensure your team remains consistently engaged in the art of crushing success.
Preventative Measures
To solidify your defense against downtime, the initial stride your team should take involves implementing preventative actions, a sometimes overlooked yet essential aspect. It is paramount not to underestimate the significance of these measures; instead, regard them as the foundation upon which your quest to minimize downtime thrives.
An example of these preventative practices is the diligent adherence to safety protocols, ensuring the well-being of your team members and averting abrupt halts in crushing operations due to unforeseen injuries. Furthermore, it is of equal importance to undertake daily assessments of the crusher’s condition, guaranteeing its consistent and high-quality performance.
Predictive Maintenance
The next crucial move to reduce downtime is the adoption of predictive maintenance. In this approach, teams use performance data to monitor and anticipate potential downtime incidents, enabling them to address issues proactively before they escalate. If your team isn’t currently monitoring operational performance, it is strongly advised to start recording this essential data.
Understanding the rate at which components and fluids in your crusher plant deteriorate and the frequency of necessary replacements can provide invaluable insights in the effort to combat downtime. Furthermore, given that your crusher plant operates under distinct environmental conditions, tracking its performance compared to industry benchmarks while adjusting critical variables can significantly enhance operational efficiency.
Once you have a grasp of your machine’s operational performance, you can proactively order replacement parts in advance, allowing you to avoid unnecessary downtime due to shipping delays. Wear parts are among the most essential components to keep readily available. Eagle Crusher understands the importance of blow bars as essential components. To help minimize downtime and control expenses, both our parts department and our network of authorized dealers are available to help you plan an optimal strategy for maintaining essential spare parts. Furthermore, Eagle Crusher’s dedicated parts department maintains an extensive inventory to expedite shipments in the event of equipment breakdowns.
Additionally, it is crucial to keep your parts in optimal condition, we strongly urge you to reach out to our parts department to explore the creation of a well-planned replacement schedule.
Understanding Your Machine
To no one’s responsibility, adhering to preventive and predictive maintenance practices can only go so far in reducing the likelihood of downtime. It affects us all and unfortunately your downtime will come. When that moment arrives, your team must be prepared to execute reactive maintenance promptly and efficiently to tackle what could potentially be a costly breakdown.
Investing in thorough training for your team members is paramount. Equipment failures tend to occur when crushing machines are pushed beyond their capacities. Adequate training can counteract overloading of crushing equipment and equip team members with the skills to effectively manage downtime incidents without exacerbating the situation.
Eagle Crusher has been tapping into the knowledge and experience of their service technicians by sharing the answers to some commons questions in their monthly “Service Questions” blogs. Join them on their journey of gaining knowledge by following Eagle Crusher on Instagram, Facebook, X (formerly Twitter), LinkedIn, or Threads, or check out the previous blogs.
Keeping Up and Crushing It
In the grand scheme of things, one of the most effective measures you can implement to reduce expensive downtime at your crushing site is to instill a culture of diligence within your team. By excelling in preventative, predictive, and reactive maintenance, your team will be well-prepared to confront the inevitable challenges, ensuring that your crusher continues to operate smoothly and safeguard your profits.