Optimizing Your Impact Crusher
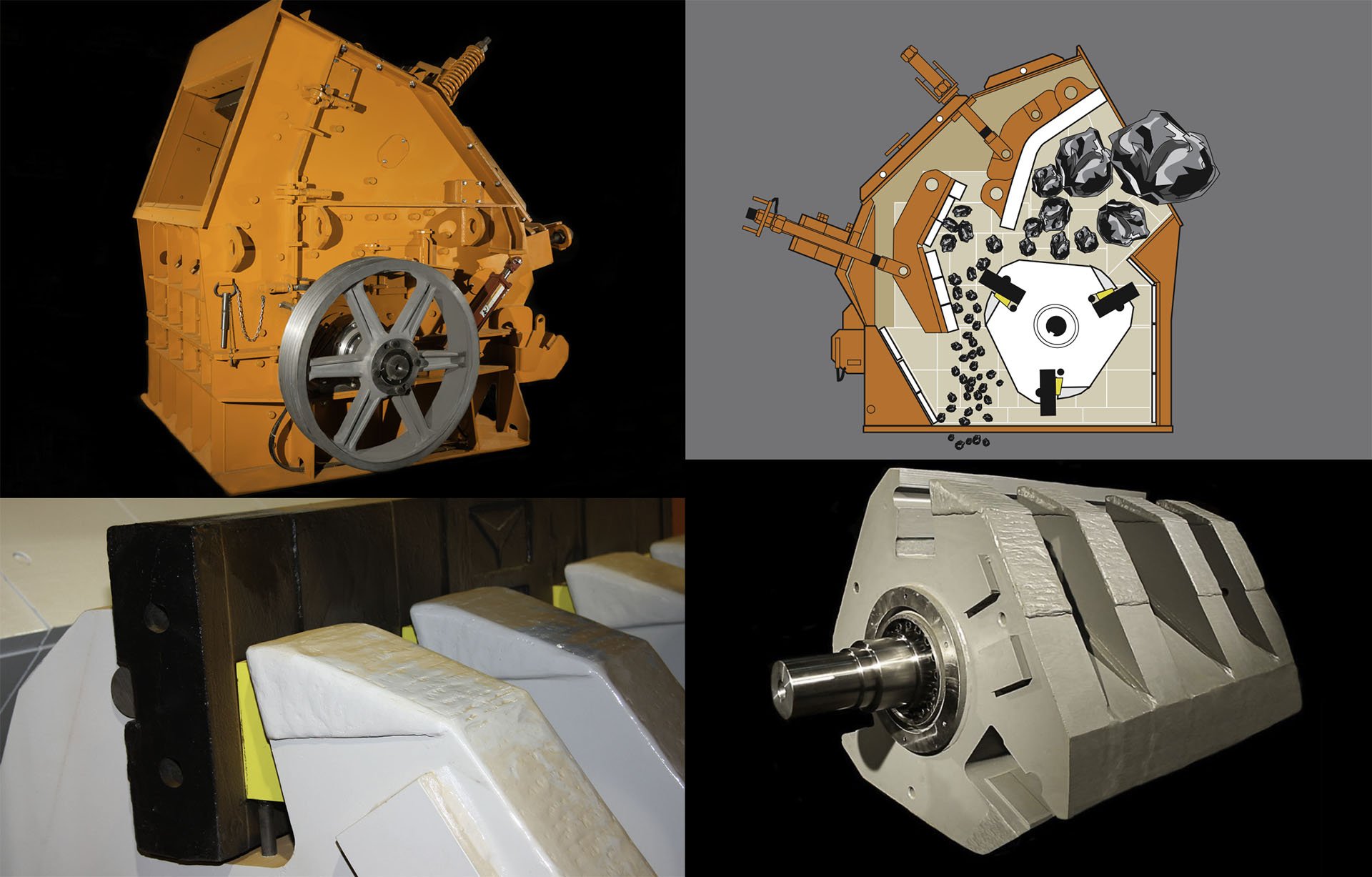
The crushing market caters to a wide range of material processing industries, like aggregate, asphalt, and concrete and demolition recycling, that handle an even wider range of materials, including limestone, concrete, and gravel, among many others. Yet, all crusher operators share a common goal: to process materials at the most cost-effective rate.
Given how many industries and materials exist, it might quickly become overwhelming to consider what the best way to optimize a horizontal impact crusher could be due to the number of variables that present themselves; however, from a fundamental perspective, it is beneficial for operators to simply focus on the apron positions of their impactors.
When a horizontal impact crusher is processing material, the aprons inside serve as supplemental points of impact as the material is smashed against them by the rotor’s blow bars. To ensure an impact crusher is operating at its most productive rate, it is valuable to take the time to configure the primary and secondary aprons so that they are working in tandem efficiently.
When adjusting apron positions, it is recommended to arrange them according to the desired output size of the material being processed by the impactor. A good rule of thumb for reducing material size is 3:1 from when it strikes the primary apron to its eventual exit, and the primary and secondary aprons should work together to facilitate this gradual reduction.
In practice, it is best to work backwards from the desired output size using the 3:1 rule of thumb. If the desired output size is 2-inch minus, it is recommended that the secondary apron is positioned to allow for that same size between it and the highest point of the rotor. Then, the primary apron is positioned to allow for 3 times that amount, so in this instance, the primary apron would be set to a 6-inch gap.
Each of these steps are taken to ensure that material is moving through the impact crusher as efficiently as possible and passing through the screen on its first go to prevent additional crushing. Keeping the impactor clear of clogs and reducing second or third passes through the crusher will increase tonnage per hour and consequently will increase profits.
As primary aprons require wrenching to adjust, it is often the case where they are left configured in their widest position, leaving the secondary apron to bear the full brunt of the impact job; this makes the impactor susceptible to clogs and needless wear. It is worth the time to adjust the primary apron into its optimal position to avoid unnecessary costs.
Another way to optimize an impact crusher is simply by investing in its regular maintenance to ensure the pieces and parts remain in good working condition. For instance, as blow bars wear, the gap between the aprons and blow bars grow, and aprons should be repositioned to account for this discrepancy.
In addition to avoiding widened gaps, maintaining and replacing blow bars as well as liners ensures more effective crushing; when everything is new, square, and flat, materials are more susceptible to being broken cleanly. For operators processing more abrasive materials, it is important to check the condition of parts more frequently.
Just as well, it can be crucial to monitor belt tension and the condition of drive belts in order to ensure that the impactor’s rotor is moving at an optimal speed. If belts are loose or worn, slipping can occur, reducing how effective the rotor is for crushing. Equally, the motor itself can be considered the heart of the crusher and should be maintained appropriately.
If you are interested in fine-tuning your horizontal impact crusher to guarantee that it is running at an optimal rate, we encourage you contact our service department. Likewise, we recommend that your crushing team contact our parts department so that the pieces and parts of your impactor remain in good condition for processing the job at hand. After all, your business profits when your impact crusher is operating at its best.
For complete UltraMax® Impactor product specifications, please visit its product page.
Serious Projects Demand Eagle Crusher.
Eagle Crusher consistently leads the industry in new product innovations. We stand by our products with unsurpassed service and support to make your job easier.
Get serious. Get Eagle Crusher.
• Durability and longevity
• 24-hour parts and service
• American made
• Highest productivity and profits
• High resale value
• Celebrating 100+ years of service