Understanding The Various Types of Blow Bars
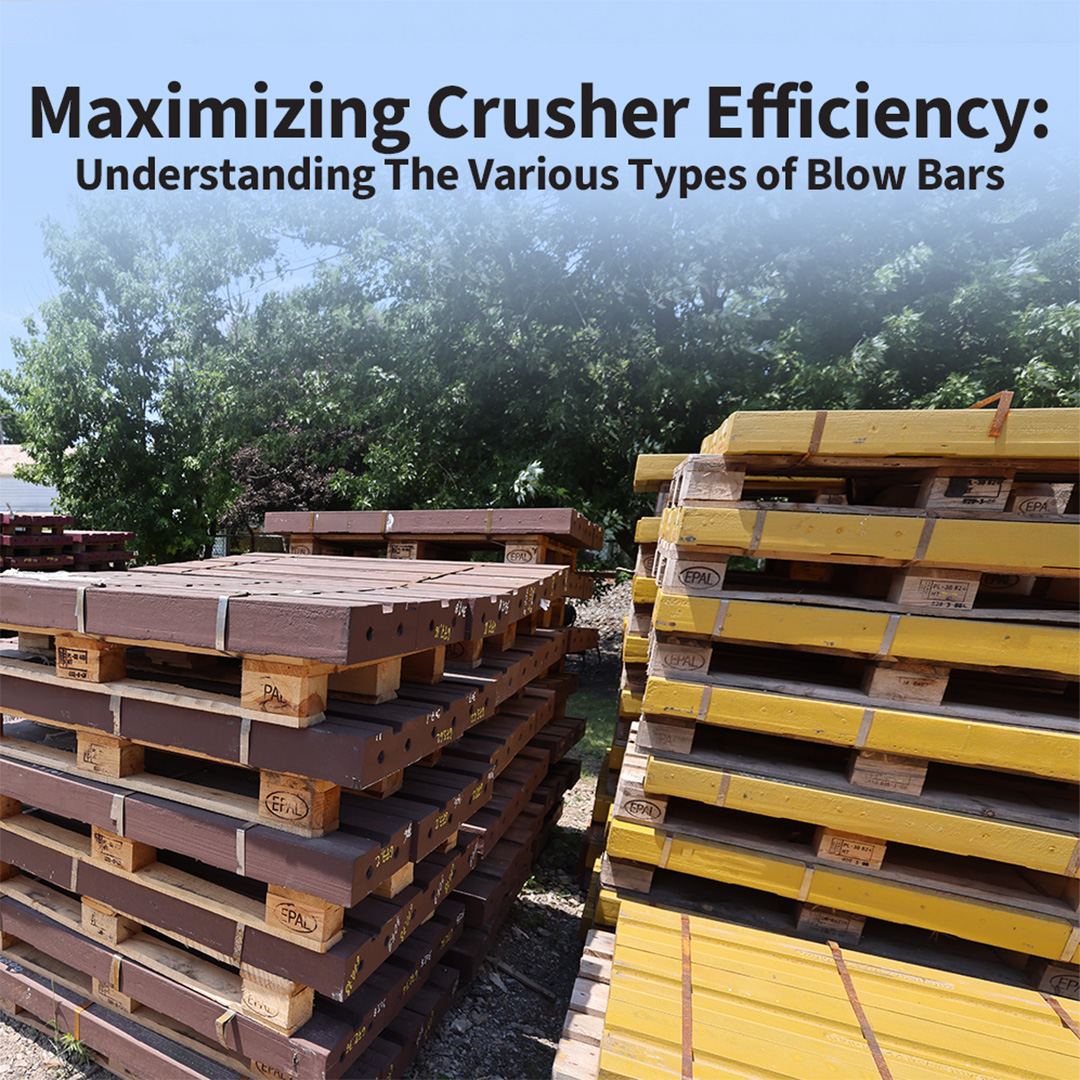
Maximizing Crusher Efficiency: Understanding The Various Types of Blow Bars
Blow bars play a crucial role in the crushing process, effectively breaking down materials like asphalt, concrete, and aggregates. Understanding the diverse metallurgies available is essential for optimizing performance in impact crushers. In this guide, we’ll explore the various types of blow bars and delve deeper into the metallurgical considerations, particularly focusing on the often-overlooked aspect of blow bar wear.
The Various Types of Blow Bars
Blow bars come in several types, each tailored to specific materials and crushing requirements. The metallurgical options include low chrome, medium chrome, high chrome, and a hybrid alloy, each offering distinct advantages in crushing applications.
- High Chrome
- Ideal for small feed sizes with minimal steel content.
- Excellent abrasion resistance.
- Commonly used as a primary in asphalt or as a secondary in applications with small feed sizes.
- High Chrome with Ceramic
- Similar benefits to high chrome but with the added advantage of increased lifespan.
- Suitable for applications with small feed size.
- Hybrid Alloy
- Combines the benefits of high chrome for abrasion resistance with fair impact resistance.
- Suited for medium-sized feed applications in asphalt or as a secondary crushing option.
- Medium Chrome
- Versatile, suitable for primary crushing in various materials like concrete, sand and gravel, asphalt, dolomite, aggregate, and limestone.
- Offers good all-around performance, allowing crushing of multiple materials with the same bar, depending on feed size.
- Medium Chrome with Ceramic
- Enhanced lifespan compared to standard medium chrome.
- Well-suited for diverse applications with medium feed sizes.
- Low Chrome
- Highly resilient to breakage, particularly effective in primary crushing applications for both recycle and aggregate.
- Ideal for scenarios where breakage is a concern with other alloys.
- Low Chrome with Ceramic
- Similar benefits to low chrome but with increased lifespan.
- Excellent for primary crushing applications where breakage is a significant consideration.
Consider Potential Wear
The amount of chrome in a blow bar influences its susceptibility to fracturing. High chrome bars are more prone to fracturing when processing materials with metal contaminants like rebar. In contrast, low chrome bars are more durable and withstand the impact of such contaminants effectively.
Choosing the right blow bars involves considering metallurgical factors, wear characteristics, and proactive maintenance. Eagle Crusher’s genuine blow bars provide a comprehensive solution to enhance your impactor’s performance and longevity. Be prepared for unexpected downtime by staying ahead with timely blow bar replacements. If you are unsure of which metallurgy is the best for your application, reach out to our parts experts and they will help you find that out.
Managing Downtime
Blow bars inevitably wear down over time due to the repetitive crushing process. Regular monitoring of wear and timely replacement or flipping of blow bars is essential to maintain high production rates. Ordering genuine blow bars from Eagle Crusher, designed by expert metallurgists, ensures a perfect fit for your impactor, extended wear life, and increased production rates.
To minimize downtime, it’s important to always have spare sets of blow bars on hand. That way you don’t have to wait for a new set to arrive when bars wear down or fracture. Reach out to Eagle Crusher’s parts department or your authorized dealer to ensure you’re always prepared.